Most Powerful Solar Panels 2022
Most Powerful Solar Panels 2022
In the solar world, panel efficiency has traditionally been the factor most manufacturers strived to lead. However, a new battle emerged to develop the world’s most powerful solar panel, with many of the industry’s biggest players announcing larger format next-generation panels with power ratings well above 600W.
The race for the most powerful panel began in 2020 when Trina Solar revealed the first panel rated at 600W. Not long after, at the SNEC PV Power Expo in China, JinkoSolar unveiled a 610W version of the Tiger Pro panel. Around the same time, Trina Solar announced that a more powerful 660W+ panel was in development. Amazingly, close to 20 manufacturers at SNEC 2020 showcased panels rated over 600W, with the most powerful being the Jumbo 800W module from JA solar. However, this panel was enormous at 2.2m high and 1.75m wide and will most likely not become commercially available.
Despite the publicity around the many high-powered panels, much of the PV cell technologies enabling these higher power ratings are universal. Traditional commercial and residential panels have also increased in size and power, with 400W to 500W panels now standard. The considerable increase in power is primarily due to increases in efficiency due to many innovations, which we describe later in the article.
Designed for utility-scale systems
The main driver for developing larger, more powerful solar panels stems from the desire to decrease the cost of utility-scale solar farms and ultimately reduce electricity prices. Since larger panels require an equivalent amount of connections and labour compared to smaller panels, the installation cost per kW is reduced, resulting in lower overall cost and decreased LCOE. As explained below, the new high-powered panels are much larger than the common ones found on residential rooftops. Although, those hoping to get a dozen 600W panels on your home rooftop to get an easy 7kW will be a little disappointed. At this stage, most high-powered panels will only be available for commercial and utility-scale systems, plus the extra-large size is not well suited and challenging to handle on most residential rooftops.
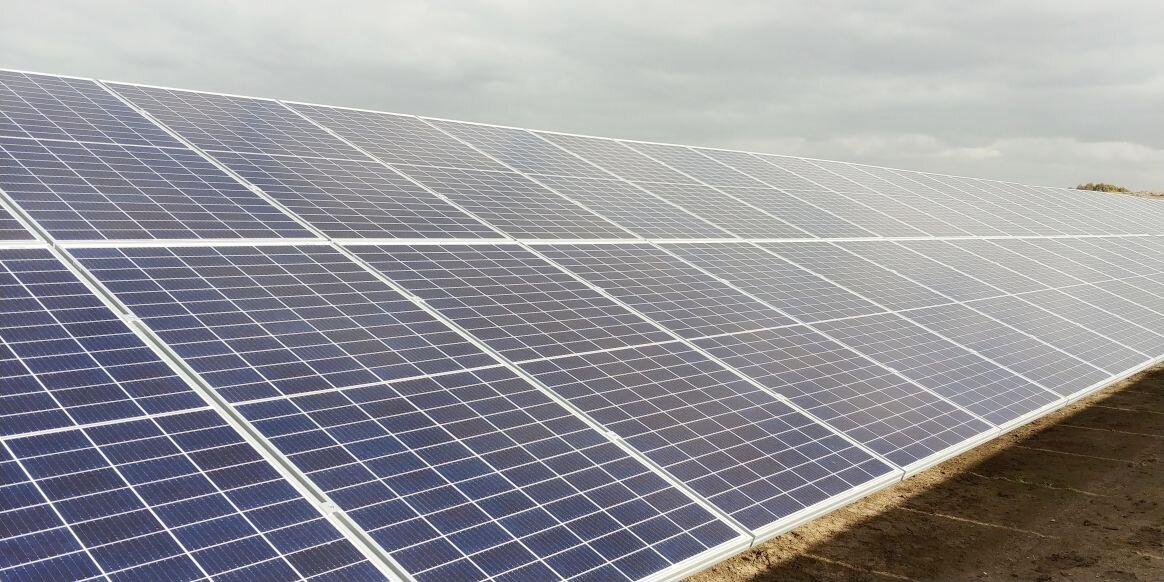
While the solar industry as a whole is slowly shifting to larger, higher wattage panels, the front runners in the race have traditionally been Trina Solar, Jinko Solar, Canadian Solar, Risen Energy and JA Solar. These well-known companies all launched ultra high-power panels with ratings above 600W over the last two years. However, more recently Jolywood, Huasun and the lesser-known company Akcome have moved forward with panels rated up to 700W utilising more efficient N-type TOPCon or heterojunction (HJT) cell technology.
Interestingly, premium module manufacturers SunPower (now Maxeon) and REC are not racing to develop larger format high-power panels. Instead, they are focusing on supplying their traditional residential and commercial customer base with high-efficiency panels. That being said, Sunpower has revealed a larger 540W panel in the next-generation ‘Performance 5’ series.
Most Powerful Solar Panels *

* List of the most powerful panels currently in production or soon to be released with a maximum panel size of 2.4m high x 1.35m wide. Availability and release dates may vary for different regions.
Make | Model | POWER | Cell size | Cell type | Efficiency % | Avail |
---|---|---|---|---|---|---|
Jolywood | JW-HD132N | 700 W | 210mm | N-Type HC TOPCon MBB | 22.5 % | Q1 2022 |
Huasun | Himalaya G12 | 700 W | 210mm | N-Type HC Bifacial MBB | 22.5 % | Q2 2022 |
Akcome | Chaser M12 132P | 700 W | 210mm | N-Type HC Bifacial MBB | 22.5 % | Q2 2022 |
Trina Solar | Vertex | 670 W | 210mm | P-Type Mono-PERC MBB | 21.6 % | Q2 2021 |
Risen Energy | Titan | 670 W | 210mm | P-Type Mono-PERC MBB | 21.6 % | Q3 2021 |
Astronergy | Astro 6 | 670 W | 210mm | P-Type HC PERC+ MBB | 21.6 % | Q1 2022 |
Canadian Solar | HiKu7 | 670 W | 210mm | P-Type HC PERC+ MBB | 21.6 % | Q1 2022 |
Yingli Solar | Mono GG | 670 W | 210mm | P-Type HC PERC+ MBB | 21.6 % | Q1 2022 |
Suntech | Ultra X Plus | 670 W | 210mm | P-Type HC PERC+ MBB | 21.6 % | Q1 2022 |
Seraphim | S5 Bifacial | 670 W | 210mm | P-Type HC PERC+ MBB | 21.6 % | Q1 2022 |
Talesun | BiPRO | 670 W | 210mm | P-Type HC PERC+ MBB | 21.6 % | Q1 2022 |
AE Solar | Aurora | 665 W | 210mm | P-Type HC PERC MBB | 21.4 % | Q2 2022 |
Jinko Solar | Tiger Pro NEO | 620 W | 182mm | N-Type HC TOPCon MBB | 22.3 % | Q3 2021 |
JA Solar | Deep Blue 3.0 | 605 W | 182mm | P-Type HC PERC MBB | 21.3 % | Q4 2020** |
Q CELLS | Q.PEAK DUO XL-G11.2 | 590 W | 182mm | P-Type HC PERC MBB | 21.5 % | Q2 2022 |
HC = Half-cut cells, MBB = Multi busbars. Maximum panel size = 2.4m high x 1.35m wide.
Larger Panel Sizes
In the past, most increases in panel power came from efficiency gains due to advances in solar cell technology. While that is partly a driver behind the massive jump in panel wattage, the main factor is the new larger cell sizes being developed together with a higher number of cells per panel. These new cell formats and configurations mean the new panels are physically much larger in size. Generally, these large panels are best suited for utility-scale solar farms or large commercial installations.
Traditionally, solar panels were available in two main sizes - the standard format 60 cell panels (roughly 1.65m high x 1m wide) used for residential rooftops, and the larger format 72 cell commercial size panels (roughly 2m high x 1m wide). Then half-cut cell panels emerged in roughly the same size but with double the amount of half-size cells at 120 cells and 144 cells. Besides the standard sizes, there were a few premium manufactures such as SunPower and Panasonic producing unique 96 and 104 cell panels.
The industry-standard panel size for much of the last decade was built around the 156mm x 156mm or 6-inch square cell format. However, the new panel sizes emerging which are up to 2.4m long and 1.3m wide are built around the larger 180 and 210mm wafer sizes. This is a size increase of 20% to 30% compared to the traditional 2.0m x 1.0m 72-cell panels which naturally corresponds to the huge boost in power per panel.
Larger Cell Sizes
To decrease manufacturing costs and gain efficiency, manufacturers moved away from the standard 156mm (6”) square cell wafer size in favour of larger wafer sizes. While there are a variety of cell sizes under development, a few cell sizes have emerged as the new industry standard; these include 166mm, 182mm and 210mm. Many of the leading manufacturers including Jinko, Longi and Canadian Solar have aligned with the 182mm format, Trina Solar is pushing the larger 210mm wafer size, while Longi, the world’s largest mono silicon wafer manufacture, is using both the 166mm and 182mm sizes depending on the application.
To remain competitive, many of the smaller volume manufactures may need to align with one of the new wafer sizes to utilise common wafer and equipment suppliers. For a complete history and insight into wafer and PV cell sizing standards, this detailed article from PV Tech examines the various wafer and ingot sizes, technology changes, and manufacturing trends around current and future PV cells.
Along with the different cell sizes, there is a myriad of new panels configurations built around the many cell combinations. The three most popular which have emerged are 66-cell (half-cut 132), 78-cell (half-cut 156), and 84-cell (half-cut 168) panels. The extra-large 210mm cells are also well suited to unique cell dividing formats such as 1/3 cut cells; where the square wafer is divided into three segments rather than the common half-cut or half-size cell.
High Efficiency Cells
To achieve these impressive power ratings the panels and cells have not just increased in size but cell efficiency has improved substantially using numerous new technologies (listed below) along with advanced rear side passivation techniques like TOPCon.
MBB - Multi-busbars
PERC/PERC+ - Passivated emitter & rear cell
TOPCon - Tunnel-Oxide Passivating Contact
N-type silicon cells
High-density cells - Reducing inter-cell gaps
Many manufacturers are exploring different ways to increase power and boost cell efficiency by spending big on research and development. The use of N-type silicon is one of the simplest ways to boost efficiency but also one of the more costly methods. However, the price gap between P-type and N-type silicon is reducing as the economies of scale lower the cost of manufacturing the high-performance N-type silicon wafers.
Chart of the maximum solar panel power trend from 2009 to 2021 - Image credit Trina Solar
MBB - Multi-Busbars
Of the many cell improvements, the most common technology used to increase efficiency has been multi-busbars (MBB). Traditional ribbon busbars (5BB or 6BB) are being rapidly phased out in favour of nine or more thin wire busbars (9BB). Some manufacturers such as REC have even moved to 16 micro-wire busbars in the new Alpha panel series. Wider cells also mean more busbars can fit across the cell surface with 10 or 12 busbars cells also becoming more common.
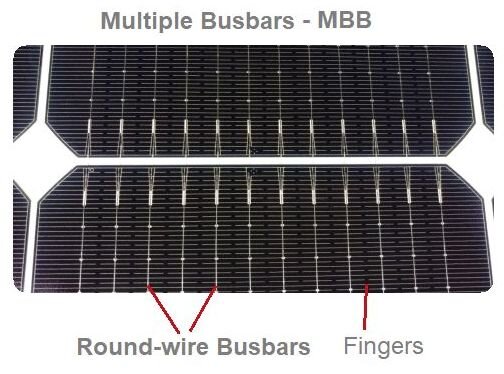
Bifacial panels featuring MBB are also growing in popularity due to the increased power output by utilising the rear side of the panel to achieve up to 20% or more power (roughly 80W extra). However, bifacial panels are generally only beneficial over light coloured surfaces such as light sandy or rocky ground used in large MW scale solar farms located in more arid areas.
High-Density Cells
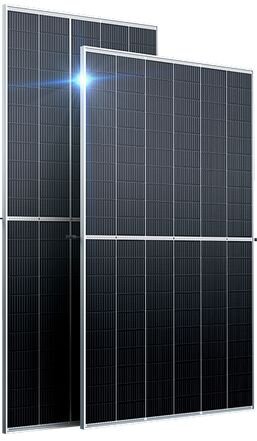
Trina Solar Vertex panels feature 210mm 1/3rd-cut high-density MBB cells - Image credit Trina
To further boost panel efficiency and increase power, manufacturers such as Trina Solar have introduced techniques to eliminate the vertical inter-cell gap between cells. Removing the typical 2-3mm vertical gaps and squeezing the cells together results in more panel surface area being available to absorb sunlight and generate power. Manufacturers have developed a number of techniques to minimise or eliminate the gap with the most common being to simply reduce the cell spacing from around 2.0mm to 0.5mm. The reason for this gap was due to traditional larger ribbon busbars requiring 2.0mm+ to bend and interconnect the front and rear of each cell. However, the transition to using much smaller wire busbars enabled the gap to be reduced significantly.
LONGi Solar is another manufacturer that managed to reduce the inter-cell gap down to 0.6mm by using what the company describes as a “smart soldering” method using integrated segmented ribbons. This new technology uses a unique triangular busbar design across the front surface of the cell, with a very thin flattened section that bends and runs behind the cell to form the interconnection.
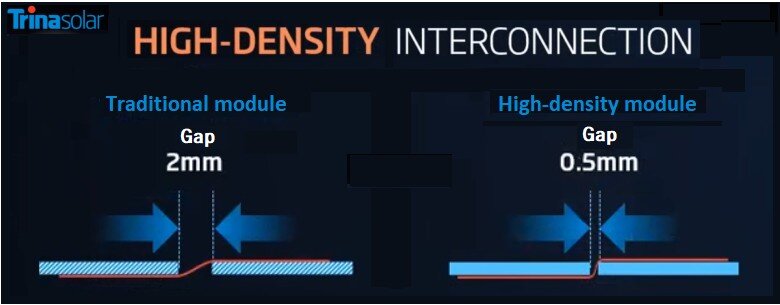
TR - Tiling Ribbon technology
Jinko Solar, currently the world’s largest panel manufacturer, developed what the company refers to as Tiling Ribbon or TR cells. Tiling Ribbon cell technology is the elimination of the inter-cell gap by slightly overlapping the cells creating more cell surface area. This in turn boosts panel efficiency and power output. The tiling ribbon technology also dramatically reduces the amount of solder required through using inter-cell compression joining methods rather than soldering. Shingled cell panels, such as those used in the Sunpower Performance series, uses a similar technology where overlapping thin cell strips can be configured into larger format high-power panels.
Increasing efficiency using Tiling Ribbon cell technology to remove the inter-cell gap - Image credit Jinko
Several other leading manufacturers such as Q Cells have taken a similar approach to boost efficiency by completely eliminating the inter-cell gap. However, most manufacturers have taken the more common approach and reduced the inter-cell clearance as much as possible leaving a very small 0.5mm gap; this effectively removes the gap without having to develop new cell interconnection techniques.
N-Type TOPCon Silicon Cells
Cells built on an N-type silicon substrate offer improved performance over the more common P-type silicon due to a greater tolerance to impurities which increases overall efficiency. In addition, N-type cells have a lower temperature coefficient compared to both mono and multi P-type cells. N-type cells also have a much lower rate of LID or light-induced degradation and do not generally suffer from LeTID (light and elevated temperature induced degradation) which is a common problem with P-type cells.
TOPCon or Tunnel Oxide Passivated Contact refers to a specialised rear side cell passivation technique that helps reduce the internal recombination losses in the cell and boosts cell efficiency. The process has been available for several years but is now becoming the new industry standard as manufacturers strive to increase efficiency and performance.
Addition Information:
the web designing company is known as the best Web development company in India.
Do you know that Online Promotion House is known for supplying the best Online promotion services for your business? SEO is very important for every type of businessman if you want to grow your business and looking for the best SEO services then an online promotion house is the best option for you
Comments
Post a Comment